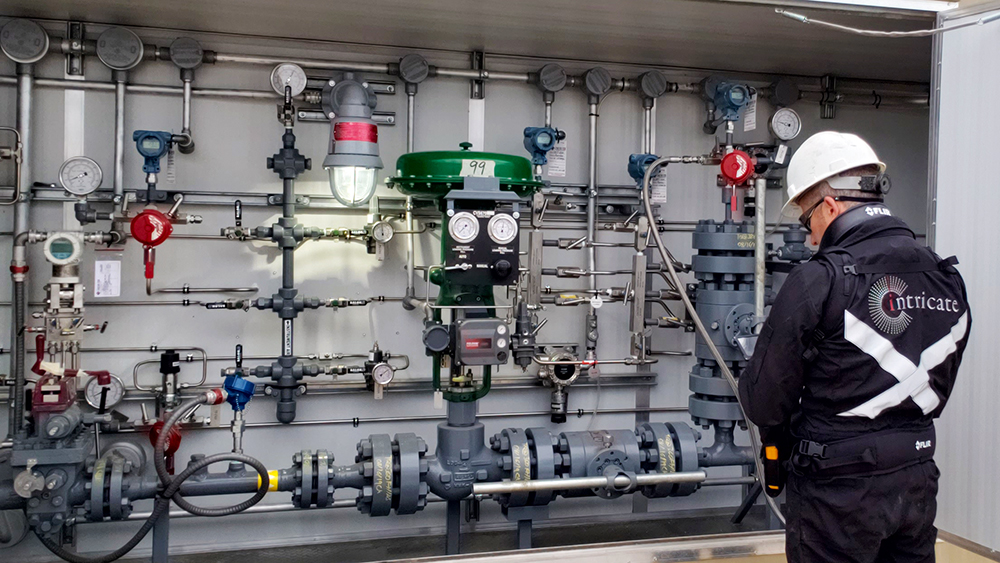
Measurement Compliance
Intricate ensures full regulatory compliance with Directive 017 through comprehensive field measurement services and proactive maintenance planning. Our skilled technicians deliver efficient, high-quality regulatory support tailored to the unique needs of each client. By strategically approaching traditionally required services, we help clients achieve immediate cost savings while driving long-term growth with precision, reliability, and cost-effectiveness.
Our services include:
- Inline meter proving (up to 6”)
- Field bench proving (up to 6”)
- Water cut verifications / calibrations
- Shop volumetric proving
- Electronic flow measurement verifications and calibrations
- Measurement schematic verifications and redlines
- FFV data verifications
- Ongoing maintenance and repair
Leveraging customized equipment and advanced field software, we offer a complete suite of compliance solutions that align with client needs and industry standards. This helps ensure operations remain efficient and are well-positioned for sustainable growth.
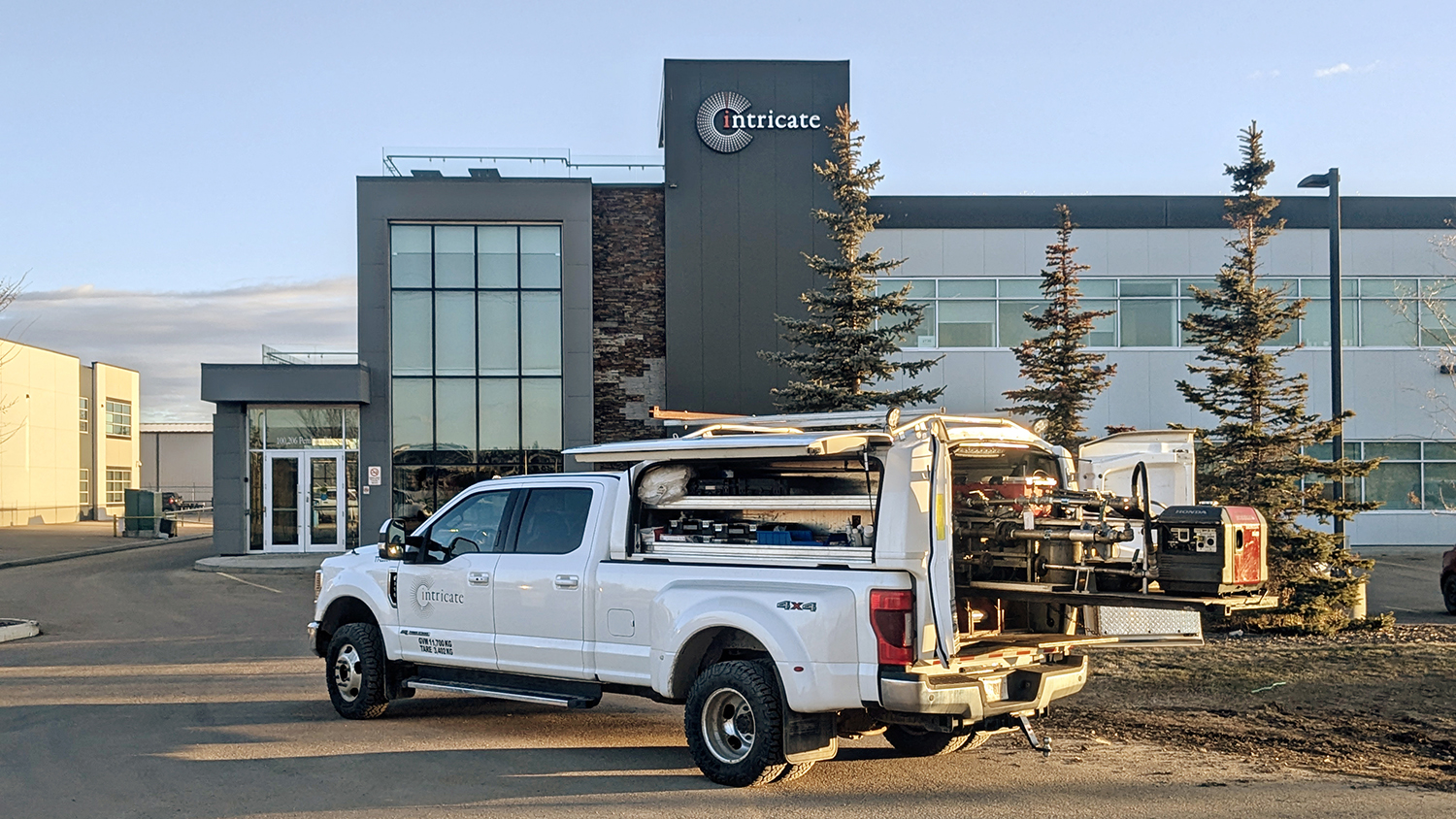
Meter Proving
At Intricate we combine advanced technology, regulatory expertise, and practical field experience to deliver reliable and efficient meter proving services. We’ve designed and built both bench and inline proving systems in-house, significantly reducing human error and standardizing the proving process. Our systems are engineered to operate without downtime, process disruption, or venting – helping clients maintain compliance while minimizing operational interruptions. Compared to traditional methods, our technology reduces proving time by 20-30%, supporting both efficiency and repeatability in the field.
We support a full range of meter configurations with:
- A fleet of mobile inline and bench provers
- Water draw equipment for verifying other proving systems
- Pipeline leak detection, monitoring, and control solutions
Our technicians are cross-trained and fully equipped to support clients across Alberta, British Columbia, and Saskatchewan. All proving systems are compliant with Western Canadian regulations, and integrated with Intricate’s proprietary software to ensure consistent, auditable results. Meter proving is a key part of our broader measurement and compliance services. Whether delivered as a standalone service or bundled with consulting, auditing, or field operations, our goal remains the same: to provide accurate, cost-effective solutions that align with our clients’ regulatory and operational needs.
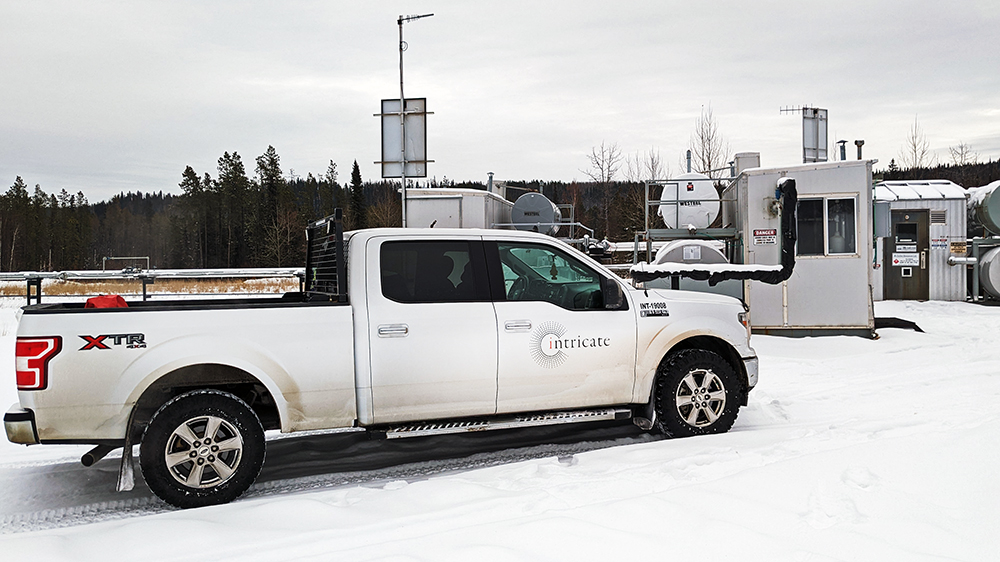
Sampling and Analysis
Intricate is committed to providing high-quality sampling and analytical services. Our qualified technicians, with extensive experience in measurement, process flow, and production processes, carry out field sampling with precision. We collaborate closely with clients to schedule exemption reviews, process improvements, and troubleshoot unique challenges.
Our gas and liquid analyses are fully compliant with Directive 017, and we provide comprehensive support throughout the analysis lifecycle. Using Intricate Solutions, our proprietary software, we track and schedule sampling frequencies to help keep your operations aligned with industry regulations.
Our services include:
- Field sampling for gas and liquids
- Compositional gas analysis
- Liquid hydrocarbon analysis
- Produced water analysis
- Trace sulfur and H2S testing
- DEOS
By optimizing sampling and analysis, we help reduce costs, increase efficiency, and ensure compliance with regulatory standards – while delivering the accuracy and consistency needed to keep your operations running smoothly.
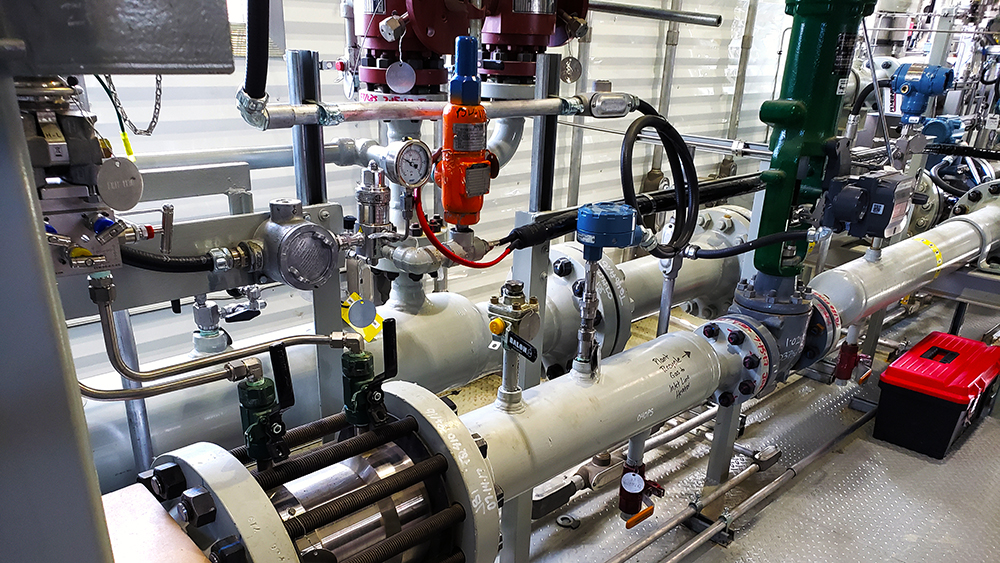
Instrumentation Maintenance
At Intricate, we offer comprehensive instrumentation maintenance services that are essential for ensuring the smooth, safe, and reliable operation of your facilities. Our team of skilled journeyman instrument technicians and electricians is fully equipped to meet the highest standards for operational reliability. Using an offline tablet application, our technicians complete electronic forms, streamlining record-keeping and providing clients with easy access to up-to-date maintenance data.
Our services include:
- Gas detection verification and calibration
- Shutdown device verification and calibration
We take an integrated approach to instrumentation maintenance, offering solutions specifically designed to align with your operational needs. Through Intricate Solutions, our proprietary software, we simplify data consolidation, maintenance scheduling, and record-keeping, ensuring that all tasks are completed on time and in full compliance with regulatory standards.